Петербургский Политех внедрил 3D-печать элементов газоперекачивающего аппарата в ПАО «Газпром»
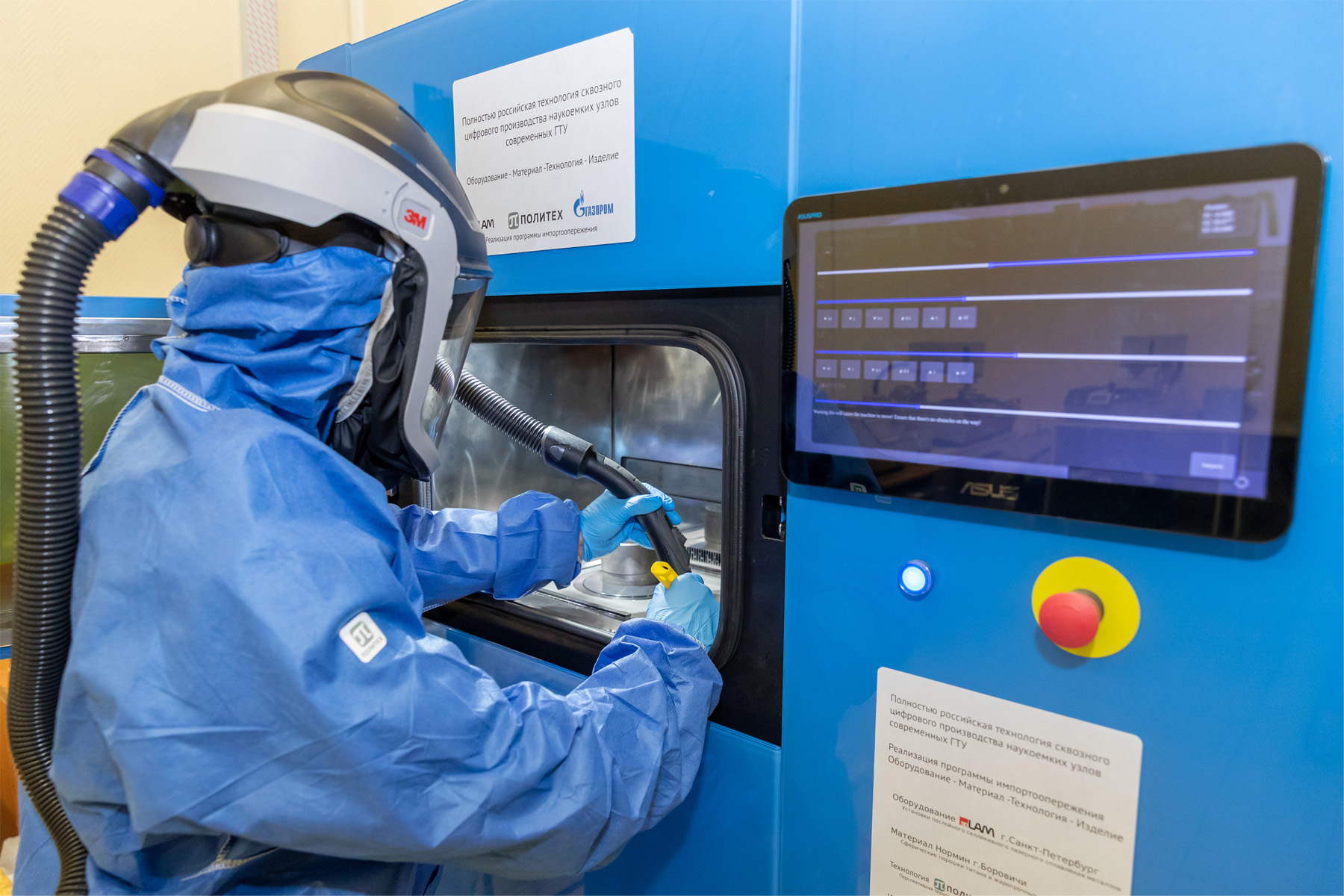
Санкт-Петербургский политехнический университет Петра Великого активно развивает аддитивные технологии. Один из ярких примеров – создание направляющих лопаток первой ступени турбовального двигателя газоперекачивающего аппарата типа ГТ-750-6 для ООО «Газпромтрансгаз Москва».
Данный газоперекачивающий аппарат является важным элементом в системе газоснабжения России. Агрегат работает при температуре до 750 °С, что требует применения прочных деталей, которые можно изготовить с помощью аддитивных технологий.
Для производства лопаток сотрудники СПбПУ использовали порошок отечественного сплава, а заготовки были изготовлены на установке селективного лазерного плавления, произведенной компанией 3DLam в России.
На этапе отработки технологии печати были проведены металлографические исследования и механические испытания, что позволило оптимизировать параметры процесса для достижения высокой плотности и минимальной пористости материала. Металлографические исследования показали, что структура металла образцов, изготовленных с применением аддитивных технологий, обладает высокой однородностью и соответствием техническим требованиям. Визуальный и капиллярный контроль не выявил дефектов, что говорит о высоком качестве полученных изделий.
«Применение аддитивных технологий позволяет не только сократить сроки и затраты на производство сложных деталей, но и существенно повысить их эксплуатационные характеристики. Современная научно-технологическая база СПбПУ позволяет нам реализовывать комплексные проекты, сочетая передовые методы печати и последующей обработки изделий», – отметил ответственный исполнитель проекта, доцент СПбПУ Игорь Полозов.
Изготовленный комплект направляющих лопаток установлен на газоперекачивающем аппарате на станции филиала «Острогожское ЛПУМГ» ООО «Газпром трансгаз Москва». Результаты эксплуатационных испытаний показали, что изготовленные направляющие лопатки пригодны к дальнейшей штатной эксплуатации.
На данном этапе СПбПУ совместно с ПАО «Газпром» готовится к расширению номенклатуры изделий, которые будут изготовливаться с помощью технологий 3D-печати, включая более сложные конфигурации и повышенные требования к физико-механическим свойствам металла.
Проект поддержан программой «Приоритет-2030» (нацпроект «Наука и университеты»).