Политех осваивает наукоемкое мелкосерийное производство изделий для ПАО «Газпром»
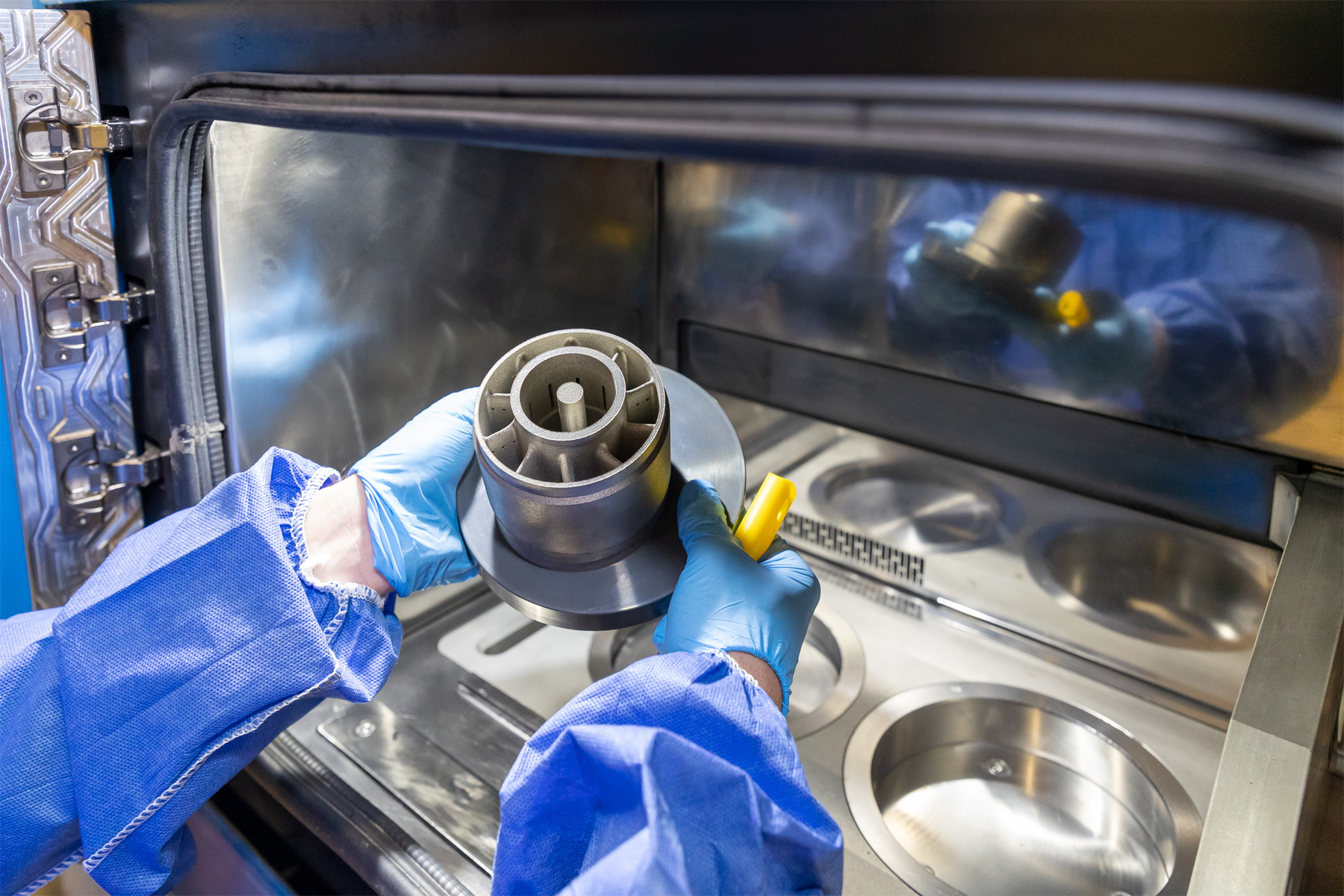
В Петербургском Политехе впервые в России разрабатывается технология для изготовления ключевых узлов стационарных газотурбинных установок, по своим характеристикам не уступающих мировым аналогам. Университет запускает производство деталей газоперекачивающего агрегата (ГПА) «Ладога 32» по заказу ПАО «Газпром» – высоконагруженные части турбины высокого давления.
«Мы провели серьезную работу с индустриальными партнерами и поняли, что многие предприятия не могут освоить наукоемкие мелкосерийные продукты по причине слишком долгих и неокупающихся инвестиционных затрат. Такие разработки не двигались дальше опытного образца, – комментирует руководитель проекта, профессор, директор Института машиностроения, материалов и транспорта Анатолий Попович. – Совместно с заказчиком мы начали искать точки соприкосновения и пришли к стратегическому решению создать наукоемкое мелкосерийное производство на базе университета. И сейчас, спустя 2 года с начала проекта, мы практически достигли уровня готовности TRL 7».
В мировой практике только начинается переход к использованию аддитивных технологий в энергетическом машиностроении, таким образом используемые в СПбПУ аддитивные технологии являются передовыми в глобальном масштабе.
В технологии Политеха в полной мере реализованы преимущества цифрового производства: минимальный брак, короткий срок освоения нового изделия (один месяц). Для сравнения, при традиционной технологии изготовления элементов газотурбинного двигателя используется печь направленной кристаллизации. При такой технологии брак составляет 70 – 80%, а на освоение нового изделия уходит 1-2 года. Кроме того, при использовании аддитивных технологий вес изделий уменьшается на 25% (достигается экономия материала), при этом срок службы изделия увеличивается в разы.
Дополнительная экономия ожидается от снижения затрат на сервисное обслуживание узлов и деталей из состава турбины высокого давления за счет использования аддитивных технологий при изготовлении запасных частей и комплектующих.
«По данному проекту мы плотно сотрудничаем с ПАО «Газпром». На первом этапе находим сложные узлы механизмов, которые требуют замены. Далее определяем объем необходимых изделий – обычно это несколько десятков изделий в месяц. В результате получаем процесс взаимодействия, который выгоден для обеих сторон – университет получает заказ на НИОКР с дальнейшим масштабированием, а индустриальный партнер решает задачу производства сложных узлов», – комментирует ответственный исполнитель проекта Павел Новиков.
Студенты СПбПУ в ходе обучения имеют возможность поучаствовать в производстве, что повышает их конструкторские и производственные навыки. Партнер, в свою очередь, имеет возможность в дальнейшем привлечь специализированные кадры из числа выпускников.
Проект по разработке высокотехнологичного оборудования послойного лазерного сплавления с селективным подогревом для мелкосерийного наукоемкого производства реализуется в рамках стратегического проекта «Системный инжиниринг» по программе Минобрнауки России «Приоритет 2030» (национальный проект «Наука и университеты»).